FOOD RECALLS TEMPLATE: PRODUCT RECALL
- A food product recall is the process of pulling out potentially harmful food products that are already on the market.
- Food product recalls can be voluntary, government-led, or company-led.
- A food product recall involves steps such as gathering information about the product in question, forming a recall plan, notifying the public, and properly handling defective products.
- In the US, food recalls are handled by the US Food and Drug Administration (FDA) and the US Department of Agriculture (USDA). FDA recalls are categorized into Class I, II, and III depending on the evaluated threat of the product.
- In the UK, food recalls are led by the Food Standards Agency.
- Food alerts are government-issued public notifications that aim to educate consumers, the affected manufacturers, and retail stores about an ongoing food recall.
- The key to smooth recall management is having the necessary information about the product through a traceability program.
- FoodDocs' Food Safety Management System offers features that can help you handle food recalls and prevent similar issues in the future.
- What is a product recall?
- What are the steps of a product recall procedure?
- What is a product recall notice?
- What could be the reason for food recall?
- UK vs. US food product recall procedure
- What are the responsibilities of food business owners in product recall?
- What are food alerts?
- How to handle food recalls with FoodDocs?
- Frequently Asked Questions (FAQs)
What is a product recall?
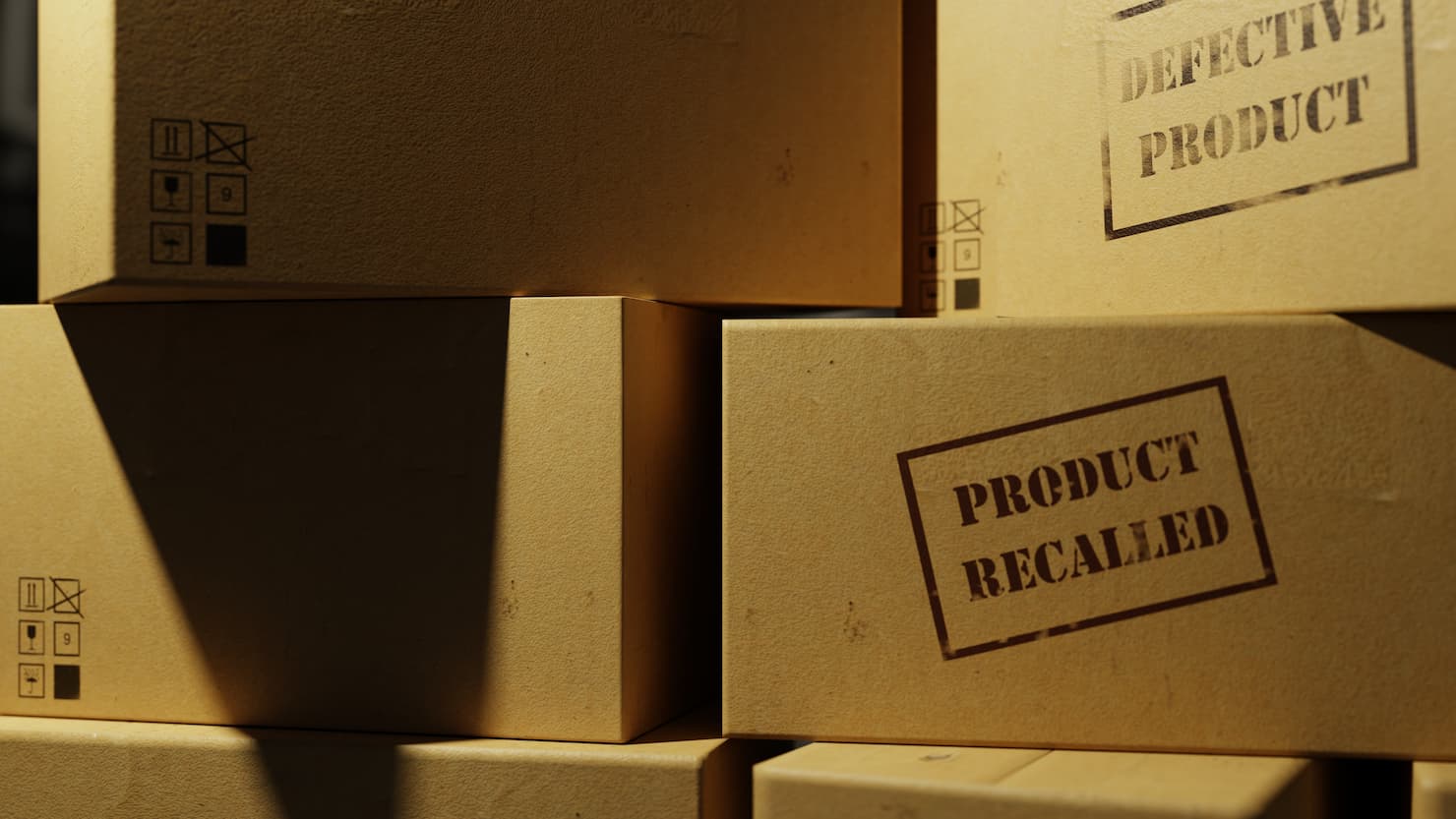
What are the types of product recall procedures?
Product recall procedures involve a list of detailed steps that are essential for minimizing the potential risk of the products being recalled. Every country has its identification and recall classification of product recall procedures.
Here are some of the most common types of product recall procedures in the food industry:
- Voluntary product recall. A voluntary recall is a result of discovering a potential product defect or food safety hazard on a food product. The manufacturer or the distributor initiates the recall. In the US, a voluntary recall is an alternative to government-initiated court action to remove non-compliant products or faulty products from the market.
- Mandatory recall or Government-led recall. As the name suggests, a mandatory recall is initiated by a government agency, such as the FDA or the Food Standards Agency (FSA), once a probable threat to public health is discovered. This recall is a legal action related to a direct violation of a particular food law and requires manufacturers to apply corrective actions to protect public health immediately. In the US, government-led recalls are split into different classes, including Classes I, II, and III, which will be discussed further in the following section.
- Firm-initiated or Company-led product recall. Any food company may order a type of voluntary recall regardless of any situation. The company-led recall does not necessarily have to be due to non-compliance with product standards and food laws. It can also be due to an internal problem within the company. Although, if a company issues a firm-initiated recall related to food safety, they are required to inform federal agencies about the situation.
Food companies are required to follow recall procedures that involve notifying the public and coordinating with local, state, and federal agencies to minimize risk exposures and safety concerns. Depending on the recall circumstances, companies may be required to provide compensation to affected parties.
The best solution for a seamless recall process of unsafe products is to ensure that all product details are properly archived and traceable. You can use our free Food Recalls Template to log the necessary information for an ongoing recall.
To save time and ensure compliance, you can use our Food Safety Management Software to log all the food information intuitively. Use our Traceability System software to access batch records, employee-in-charge, and production dates. You can also use our automatically generated monitoring logs to analyze the root cause of the recall.
What are the steps of a product recall procedure?
In the case of a food product recall, concerned food safety agencies will conduct health hazard evaluations to determine the extent of the potential threat. If your food business is faced with a mandatory recall procedure, your recall team must have an effective recall plan or strategy prepared to address the situation at hand.
Here are the essential steps to take during a food product recall situation:
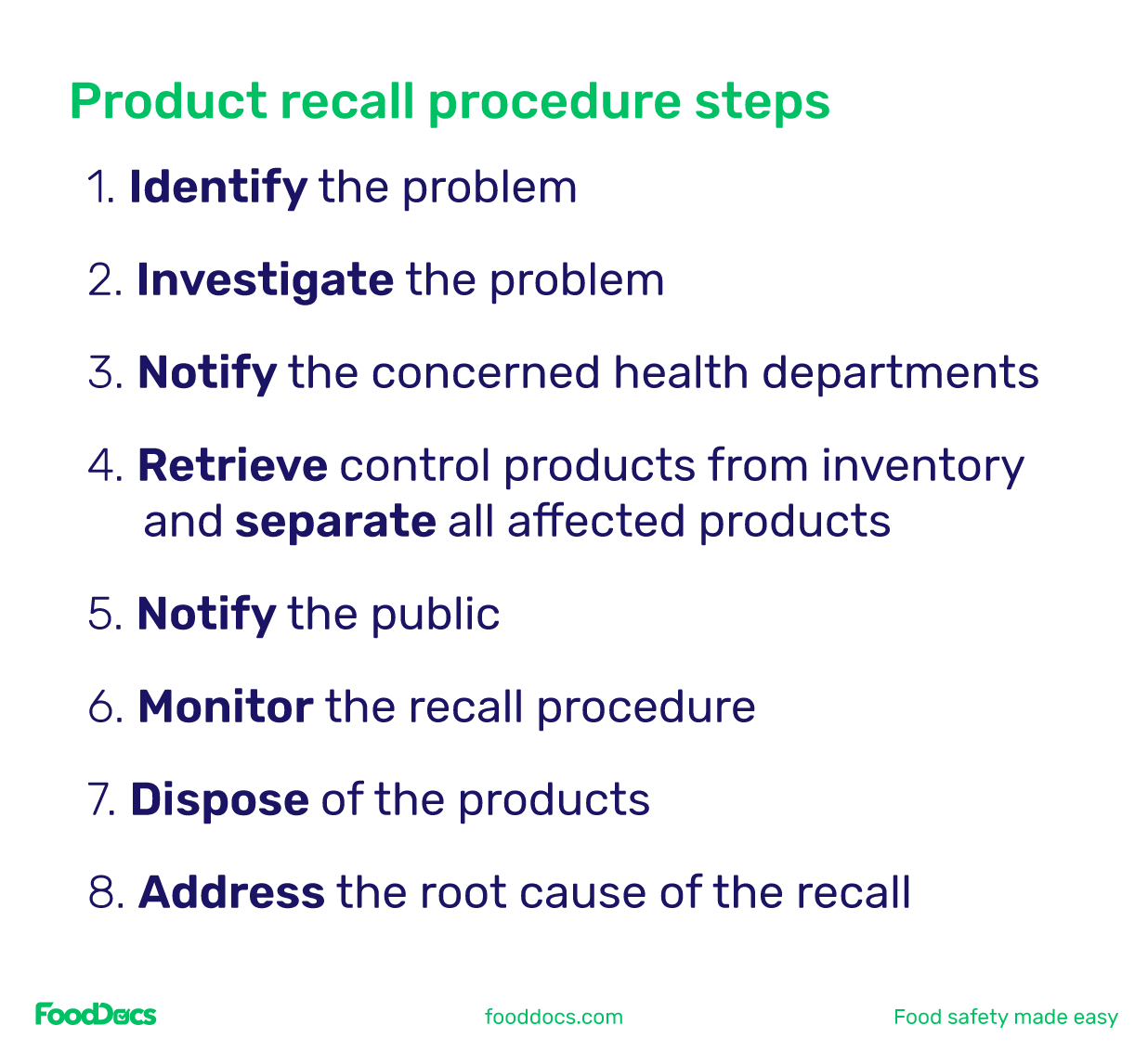
General steps for a product recall procedure
Step 1. Identify the problem
The first step in a recall procedure is determining if the product poses a potential threat to public health. If a complaint is filed against your product, and this triggers a potential recall, your team must be able to review and gather information about the product quickly.
At this stage, information, such as the defect or issue being complained about, the name and batch of the product, and product codes, must be gathered. All supporting documents that will help you trace its production must be available as well. Your recall team must be able to coordinate with the affected markets or customers during the food incident.
Step 2. Investigate the problem
The investigation step involves analyzing the whole process that the product has undergone until it is distributed to the market. Your team must be able to access production records, monitoring logs, and checklists related to the product's processing.
During the investigation, your response team must determine the following information:
- scope of the problem,
- the potential risk of the defect or degree of health hazard,
- the root cause,
- the number of affected products, and
- the affected distribution channels.
Step 3. Notify the concerned health departments
Once your food safety team has collected the information about the food incident and the concerned product, your team must immediately notify the correct health and safety departments.
The concerned health agency will evaluate the information you submitted. Your team must be fully transparent with the gathered data to help the agency determine the scope of the recall. The food safety agency will also require an appropriate product recall strategy from your end, which they will evaluate.
During this stage, you must also notify all distribution channels that may be affected by the product and request their aid in the recall.
Step 4. Retrieve control products from inventory and separate all affected products
All stocks must be held for further investigation and separated from the wholesome batches to prevent further release of the unsafe product. Control batches must also be submitted for analysis.
If a machine defect causes the recall, all products that were processed using the defective machine must be isolated. At this stage, your food safety team must closely coordinate with the food safety agencies.
Step 5. Notify the public
During the recall process, the recalling business must immediately notify the public and affected channels about the food incident. A public notice indicating the product in question, the cause of the recall, affected product units, and appropriate actions to contain the problem must be communicated to the public.
Step 6. Monitor the recall procedure
Your food business team handling the recall is required to submit periodic recall status reports to the concerned health departments. This step will help you determine if the recall is under control and which areas need more attention.
A current recall status report typically includes the following information:
- The number of informed channels.
- The number of currently recalled batches.
- Distribution channels that did not respond to the recall notice.
- The evaluated effectiveness of the recall plan.
- The estimated time needed to complete a recall plan.
Once the food safety agency issues the termination of the recall process, your team is no longer required to submit reports.
Step 7. Dispose of the products
Defects, non-compliance in processing, or the presence of food safety hazards often cause food recalls. In this case, the best course of action is to dispose of the affected products. Product disposal must be properly documented.
In case of recalls due to mislabeling on the product packaging or design defect, the affected food items may be repacked.
Step 8. Address the root cause of the recall
Once the entire recall process has concluded, your team must communicate the food incident to the entire business. At this stage, the root cause of the problem must be addressed to prevent similar incidents in the future.
A proper corrective action plan that is fit for the root cause of the recall must be established and executed.
A complete monitoring and traceability system are keys to addressing a recall case efficiently. Information is key when handling a recall procedure. If your team can effectively access the necessary information about the affected products, they can proceed with all the steps of a recall procedure without any problem.
What is a product recall notice?
A product recall notice or food recall notice is an official statement released by a company or a food regulatory agency concerning a product recall. The recall notice aims to minimize the potential effects of the affected product or food incident by notifying the general public and distribution channels about the recall.
A recall notice includes important information, such as:
-
- A description of the product being recalled
- The reason for the recall, including the specific issue or hazard
- The potential risks or harm associated with the product
- Instructions for consumers on what to do if they have purchased the product, including how to return or dispose of it
- Contact information for the company or regulatory agency responsible for the recall
Recall notices are distributed through different modes, including the media. In the US, food recalls are published under the FDA Enforcement Report, whereas the UK government publishes recall reports on the Food Standards Agency website.
What could be the reason for food recall?
Most of the causes for a food recall are found during the company's food safety or federal inspections, HACCP audits, or analysis of foods. In some cases, recalls can be the result of food contamination, unintended adulteration, or as simple as a slight quality issue.
There could be several reasons, but here are the most common reasons behind food recalls are following:
1. Contamination by pathogens. This is one of the most common reasons for food recalls. In cases of foodborne illness outbreaks, a wide range of food recalls is often issued to protect public health. Cross-contamination by elevated levels of biological hazards can occur at any point in the process. Common causes of recalls include potential Salmonella contamination or E. coli and Clostridium botulinum.
2. Food contains physical contaminants. In addition to the presence of pathogens, the detection of foreign materials, such as broken glass, is also a leading cause of food recalls. Sharp or hard items found in food products can cause significant injuries to affected consumers.
3. Allergen mislabeling. Failure to declare or mislabel a present allergen is a major violation of food laws. Major food allergens can put the lives of consumers with an allergy at risk if consumed.
Use our downloadable Food Allergen Chart to help you manage the major food allergens in your business.
4. Undeclared ingredient. This can happen if an ingredient is accidentally left out of the labeling or if the manufacturer changes the formulation of the product without updating the package label.
5. Misbranding. If a product fails to meet labeling requirements by a regulatory agency or if the product is marketed in a misleading manner, it can be subjected to a food recall.
6. Adulteration. Detection of unintentional or intentional adulterants that food safety agencies do not approve can result in a food recall. Food adulteration is the addition of substances to change the characteristics of a product.
7. Packaging defects. If a product's food packaging has been compromised or is found to be non-compliant with minimum food safety standards, the contained product may also be compromised.
8. Detected equipment malfunction. If your team detects that an equipment defect affected a batch of your products, this case may lead to contamination or other food safety issues. The affected products must then be recalled.
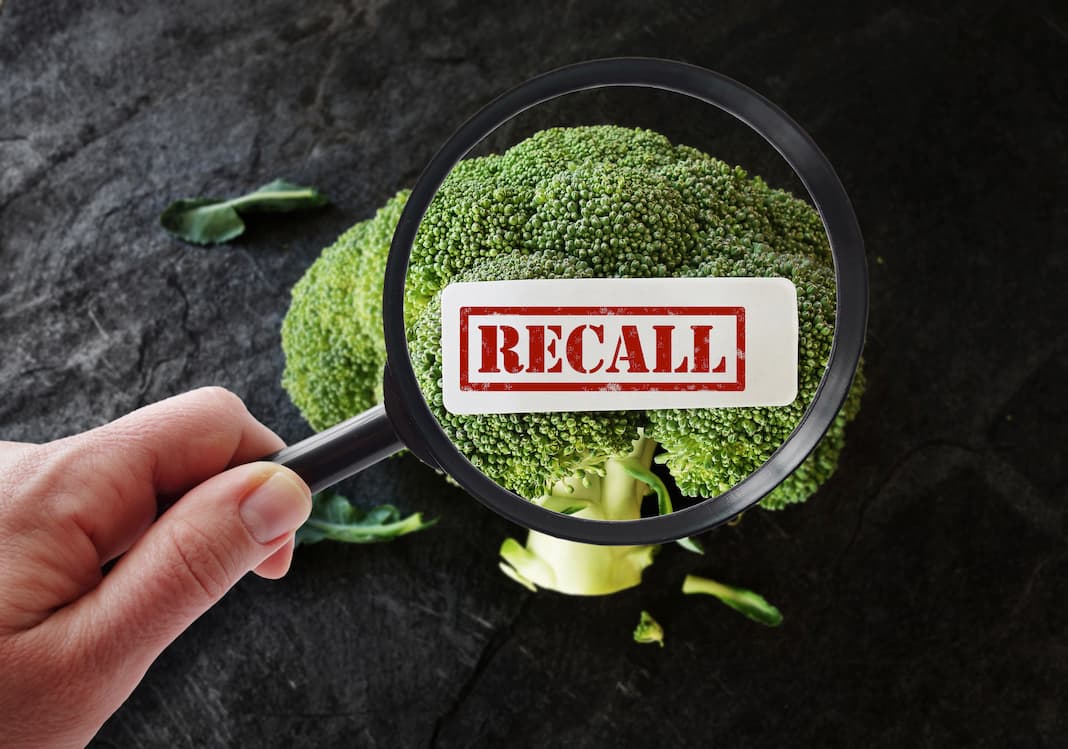
Food recalls are crucial for protecting public health and safety, and they are taken very seriously by regulatory agencies and food manufacturers. When a recall occurs, it is important for food handlers and business owners to follow the instructions provided to minimize any potential health risks. By being aware of the reasons for a food recall, food handlers can make informed decisions on the necessary removal actions during a recall.
It is also important to note that countries may have their regulations regarding food recalls. Differences in regulations for addressing food recalls may focus on the necessary steps to take, the information to collect, and the corrective actions to apply.
In the next sections of this article, we go into detail on the difference between the product recall procedures in the US and the UK.
UK vs. US food product recall procedure
While the goal of a food recall is universal, the procedures and regulations for food product recall can vary widely between different countries. The United Kingdom (UK) and the United States (US) both have strong systems for food product recalls, but there are some key differences in how they are handled.
One key difference between the UK and US food product recall procedures is the level of authority that regulatory agencies have in ordering a recall. In the UK, the FSA has the authority to order a recall, while in the US, the FDA can order a recall but also relies on voluntary action initiated by food businesses.
Here are some highlights of the difference between the UK and US food product recall procedures.
Food recall | United Kingdom | United States |
Presiding food agency |
Food Standards Agency |
|
Recall classification |
*Classes vary in urgency |
*Classes vary in depth of hazardous effects |
Public notification | Food business directly notifies the public | Food agency handles public notification |
Reference food safety regulations |
In the following sections, we will discuss the different food recall procedures in each country.
UK product recall
Food product recalls in the UK are guided by Regulation (EC) No. 178/2002. Under this regulation, food products shall not be placed on the market if it is unsafe and poses a risk to health and public safety. The regulation also provides key points in determining the safety of foods.
Under the food regulation to follow, determining whether a food product is safe to consume depends on the following factors:
-
- The accuracy of the product concerning its intended use.
- The correctness of information provided for the consumer, including information on the label concerning ingredients that can potentially cause adverse health effects.
- The presence of contaminants can cause immediate, short-term negative effects or chronic illness in the public and the following generations.
- The presence of potential cumulative toxic effects.
- The presence of allergenic components.
The regulation serves as a guide on when to trigger a withdrawal or recall if a manufacturer has any reason to believe that a product was produced, imported, processed, or distributed against regulatory compliance.
Below, we discuss more on how food product recalls, and market withdrawals are executed in the UK with the following topics:
- What are the product recall procedures in the UK?
- How to create a product recall procedures template in the UK?
- What are product recall examples in the UK?
What are the food product recall procedures in the UK?
Food product recalls in the UK are managed and monitored by the Food Standards Agency (FSA) and local health departments. In case of a food incident where the food is no longer under the control of the manufacturer, all affected food business operators are required to cooperate and help determine if the food is unsafe for consumption.
A food product recall procedure in the UK initiated by the FSA consists of the following steps:
- Identify and assess if there is a problem
- Perform a risk assessment
- Plan a food withdrawal or recall
- Establish a team to oversee the food withdrawal/recall
- Gather information about the food product
- Notify food regulatory bodies, suppliers, and business customers
- Remove the products from the market
- Monitor the progress
- Handle unsafe food
- Rework unsafe food
- Dispose of unsafe food
- Conduct root cause analysis
- Review food withdrawal/ recall procedure
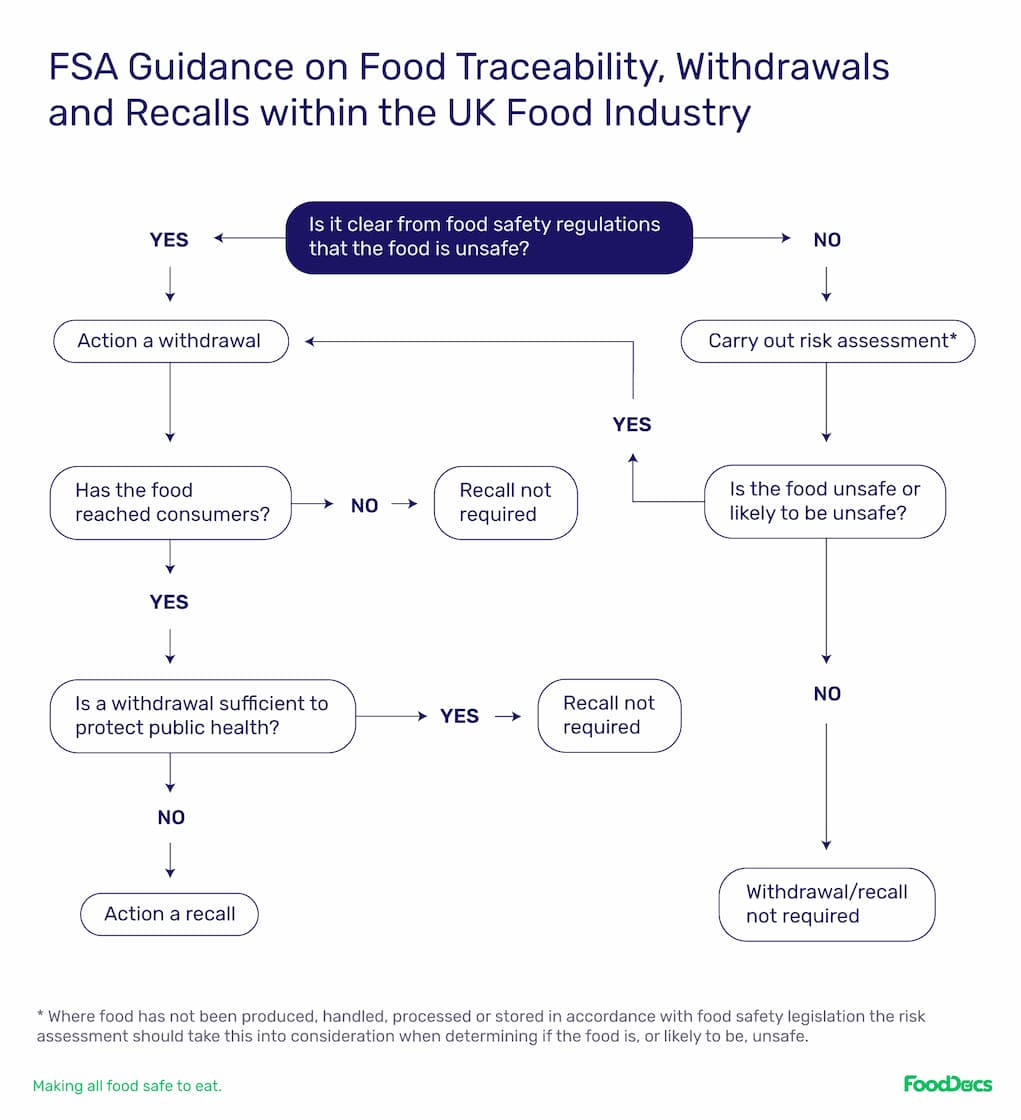
FSA guidance on food recalls
Overall, the aim of food product recall procedures in the UK is to ensure that consumers are protected from potentially dangerous or contaminated food products and that food business operators take responsibility for their products.
How to create a product recall procedures template in the UK?
In the UK, while the FSA provides guidance on how to conduct a food recall and create public health alerts, there is no strict format for a recall template. However, creating a product recall template is a vital step in preparing your business to handle a recall effectively.
To create a product recall procedure template, include the following parameters:
1. Manufacturer and product information. Include the necessary basic information about the product, including the name, address of the manufacturing company, and affected.
2. Food recall stages. According to the major food recall procedures, list each stage in separate rows. This will help you get a clearer view of your progress along the recall process.
3. Food recall tasks. Under each stage, list all of the essential tasks that will help measure the completion of a recall stage. Make sure that each task is measurable.
4. Reason for recall. Indicate a detailed explanation or key information about the reason for the food recall. If you are using a digital template, attach all necessary files.
5. Employee in charge. Use this section to identify the contact person in charge of a particular task. This will also help you better manage your recall committee.
6. Date of completion. Under this section, the person in charge must note when the task was done. This information is essential when making recall reports as mandated by food regulatory agencies.
7. Corrective actions. In addition to the major corrective action report, the recall committee must note any corrective action performed to aid in the recall procedure.
8. Remarks or important notes. Use this column to note that the head of the recall committee verified the information or to add other essential notes.
You can use our free Recall Template to help you keep track of your entire recall process. This template is flexible and can be printed repeatedly for your convenience. Provide our email address and click on the download button to get a free copy of our Recall Template.
What are product recall examples in the UK?
In the UK, the potential presence of allergen contamination remains the main cause of food and drink recalls. Food allergen-related recalls peaked in 2019 with a total number of 118 cases and decreased to approximately 80 in 2021. According to recent food safety news, around 50% of the issued food recalls in the UK from 2016 to 2021 were related to food allergens.
Below are some major food product recall examples that occurred in the UK:
In 2019, a deadly outbreak of Listeria was linked to pre-packaged sandwich products and salads sold by a company called The Good Food Chain. The foodborne disease outbreak resulted in several deaths and led to a major recall of products from retailers and hospitals across the UK.
In April 2023, the company Melting Moments recalled batches of its Melting Moments Frosted Carrot Cakes. The recall was issued after detecting that the products contained peanuts, which were not indicated on the label. The products were identified as a potential health risk to consumers with peanut allergies.
A case of undeclared brazil nuts prompted the company Rude Health to recall batches of its Organic Ultimate Muesli products in 2023. The product labeling did not contain any indication or warning that the food allergen was present.
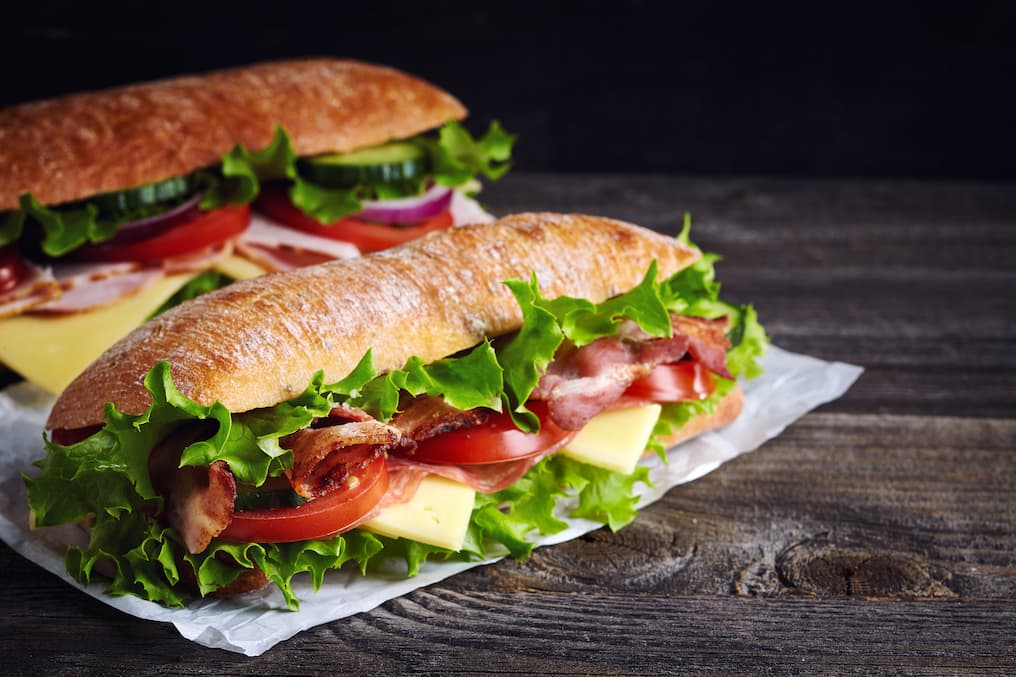
In May 2023, Müller recalled batches of Cadbury dessert products from the market as a precaution. The products were suspected of having Listeria contamination possibly. The company immediately released a food recall notice that contained guidance instructions for customers who bought the products.
US food recall
In this section, we discuss the following topics on food recalls in the US:
- What are the FDA recalls?
- What are the food recall procedures in the US?
- How to use the FDA recall plan template?
- Recall examples of whole foods and other products in the US
Food recalls procedures in the United States aim to help protect public health and safety by implementing a system that efficiently identifies and removes potentially hazardous products from the market.
In the US, the FDA and the US Department of Agriculture (USDA) are mainly responsible for overseeing recalls regarding products manufactured in the US. Recalls in the US are subject to investigation based on the regulations established under the FD&C Act. In addition to the FD&C Act, several other laws and regulations can apply to food recalls, depending on the specific circumstances of the recall.
What are the FDA recalls?
FDA recalls, as the name suggests, are recall orders initiated by the U.S. Food and Drug Administration after finding substantial evidence that a product poses a risk to public health. The FDA has the authority to regulate a wide range of products, including food, drugs, medical devices, cosmetics, and tobacco products. It can initiate recalls for any of these products if they pose a risk to public health.
FDA recalls can be classified into three different categories based on the level of risk they pose:
-
Class I. These are the most serious type of recall, and they are initiated when there is a reasonable probability that the use of, or exposure to, a product will cause serious adverse health consequences or death.
-
Class II. Class II recalls are initiated when the use of, or exposure to, a product may cause temporary or medically reversible adverse health consequences or when the probability of serious adverse health consequences is remote.
-
Class III. Recalls under this class involved products with minor violations that are not likely to cause adverse health consequences.
The classification of recalls by the FDA is the result of intensive health risk assessment. The agency works closely with food manufacturers and distributors in evaluating the potential risk of a product in question. The FDA also maintains a database of all product recalls it has initiated, which can be accessed by the public.
What are the food recall procedures in the US?
Food recalls in the United States are critical for protecting public health, and there are specific procedures that must be followed to ensure the safety of consumers. The FDA and USDA have established guidelines and processes for identifying and investigating potential food safety issues, classifying recalls based on severity, notifying the public and industry, and removing potentially harmful products from the market.
The common steps for a food recall in the US usually include the following:
- Build a recall team
- Identify the problem
- Investigate the problem
- Conduct a health hazard evaluation
- Determine the scope and depth of recall
- Notify the food safety agencies, distributors, and consumers through a recall notice
- Control or dispose of the product
- Conduct an effectiveness check
- Conduct recall simulations
- Monitor the recall process
- Reevaluate the recall/ withdrawal activity
By following these procedures, the agencies can quickly remove potentially harmful products from the market and prevent further risks to public health. While no system is perfect, the food recall procedures in the US represent a vital effort to maintain the safety and quality of the food supply chain and to protect the health and well-being of consumers across the country.
How to use the FDA recall plan template?
While the FDA provides a detailed guide on how to create a recall plan, your own food recall response team must review the plan and tailor the procedures to your product specifications.
The FDA provides draft guidance for the food industry that aims to help food manufacturers in handling recall procedures. The guide indicates the general requirements for a recall plan and supplementary resources in creating one.
In general, the recall plan guide includes the following sections:
- Requirements for a recall plan with preventive controls. The template indicates the necessary actions to take in case of violation according to the preventive controls rule. The rule includes requirements for making a written recall plan, the responsibilities of each personnel, and the information needed to inform the public about the recall.
- Instructions for creating a recall plan under 21 CFR 117.139(b)(1)
- A complete listing of product information
- Recalling firm information
- Reason for the recall (Model recall letter (21 CFR 7.49(c)(1)(iii))
- Health hazard assessment
- Procedures to be taken to perform recall actions. The guide describes the steps on how to execute a recall plan in the most efficient way. It includes recommendations on which channels to course the notifications through and the information needed for an effective recall process.
- Notification instruction for direct distributors under rule 21 CFR 117.139(b)(2). Can be done through letters, email, telefax, or text messaging.
- Instructions on what to do with the products
- Remove food from sale
- Cease distribution
- Notify customers
- Return food to the manufacturer/ properly dispose
- Open communication channels for recipients
- Steps in conducting an effectiveness check to verify the level of information received by affected stores and consumers.
- Procedures in assigning responsibility for recall actions. The guide defines the critical jobs during recalls and identifies candidates fit for the position. It also lists the necessary information about the employee to note. Knowing who to communicate with can help improve the efficiency of the process. Some of the major roles for a recall procedure include:
- Recall coordinate
- Distribution
- Production and quality assurance
- Consumer affairs
- Public relations
- Marketing
- Regional sales manager
- Procedures for notifying the FDA. The FDA guide includes a list of criteria to help identify the food incident's urgency. It also includes which FDA channels to contact in case of a recall.
A recall response plan is a vital part of a company's Food Safety Plan. Together with a Traceability System and Corrective Actions Plan, they form a program that ensures complete transparency and preparedness in your production chain.
Recall examples of whole foods and other products in the US
In the US, some of the leading causes of food recalls include biological contamination and problems with food packaging. The latter cause includes mislabeling, misleading information, undeclared major allergens, and errors in the food product label.
Here are some examples of recent major food recalls in the US:
In 2019, more than 132,000 pounds of ground beef and beef burger patties produced by a Colorado-based company were recalled due to possible E. coli contamination. The products were sold under various brand names and were distributed to retailers and institutions in several states. The contamination was discovered during routine testing by the USDA's Food Safety and Inspection Service (FSIS).
Tyson Foods issued a recall in October 2021 for 8.5 million pounds of ready-to-eat chicken products due to potential Listeria contamination. The affected products, produced between December 26, 2020, and April 13, 2021, were distributed to various institutions nationwide. This recall was classified as a Class I recall, indicating a high risk of serious health consequences or death if the product is consumed.
In 2022, the FDA and CDC presided over the investigation of the multistate outbreak of Salmonella Senftenberg infections that were associated with certain Jif peanut butter products. The implicated company, J.M. Smucker Company, voluntarily recalled the potentially affected products.
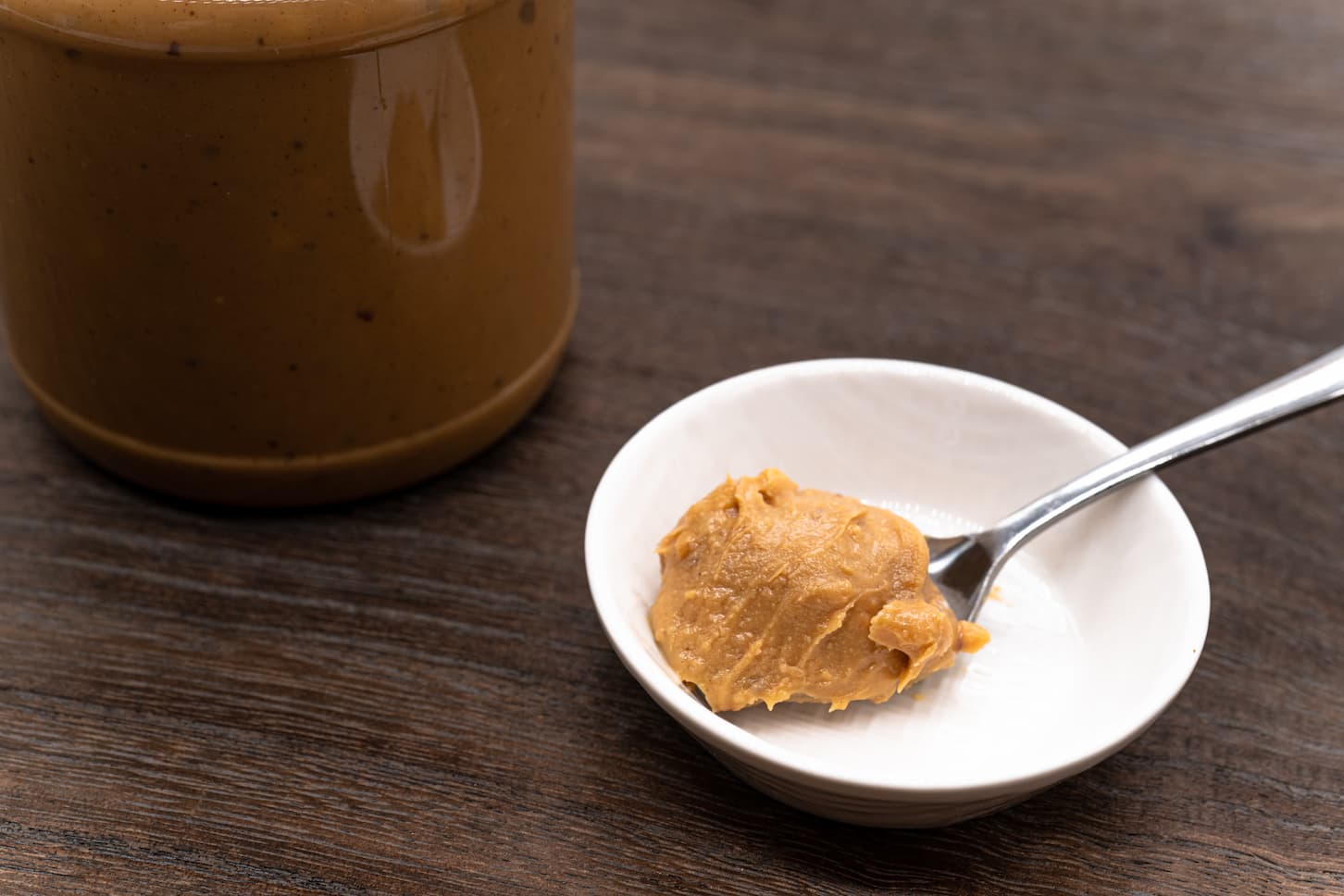
What are the responsibilities of food business owners in product recall?
Food business owners play a great role during a food product recall. In most cases, the food business owner has direct control and coordinates with food regulatory bodies in handling the recall. They act as the senior recall manager.
Some of the major responsibilities of a food business owner in case of a food recall include the following:
- Create a recall response team with defined roles and responsibilities
- Ensure proper documentation of every recall decision and step
- Make sound and data-driven decisions that will protect public health from hazards
- Inform federal, state, and local food safety agencies about the recall
- Supervise the entire recall process
- Re-evaluation of the recall process to form a stronger recall plan
A food business owner does not have to manage an entire food recall process solely. Delegating the different tasks in a food recall can help ensure that the process will be successful and problems will be minimized.
To help you ensure that all product and process information is secured and efficiently accessible, use FoodDocs' intuitive Food Safety Management System. Our system features a Traceability System that helps you log all product information, such as batch number, involved employees, production dates, and other essential data, in one place.
In addition, our smart software can help you ensure that process parameters are always monitored and logged using automatically generated monitoring logs and checks.
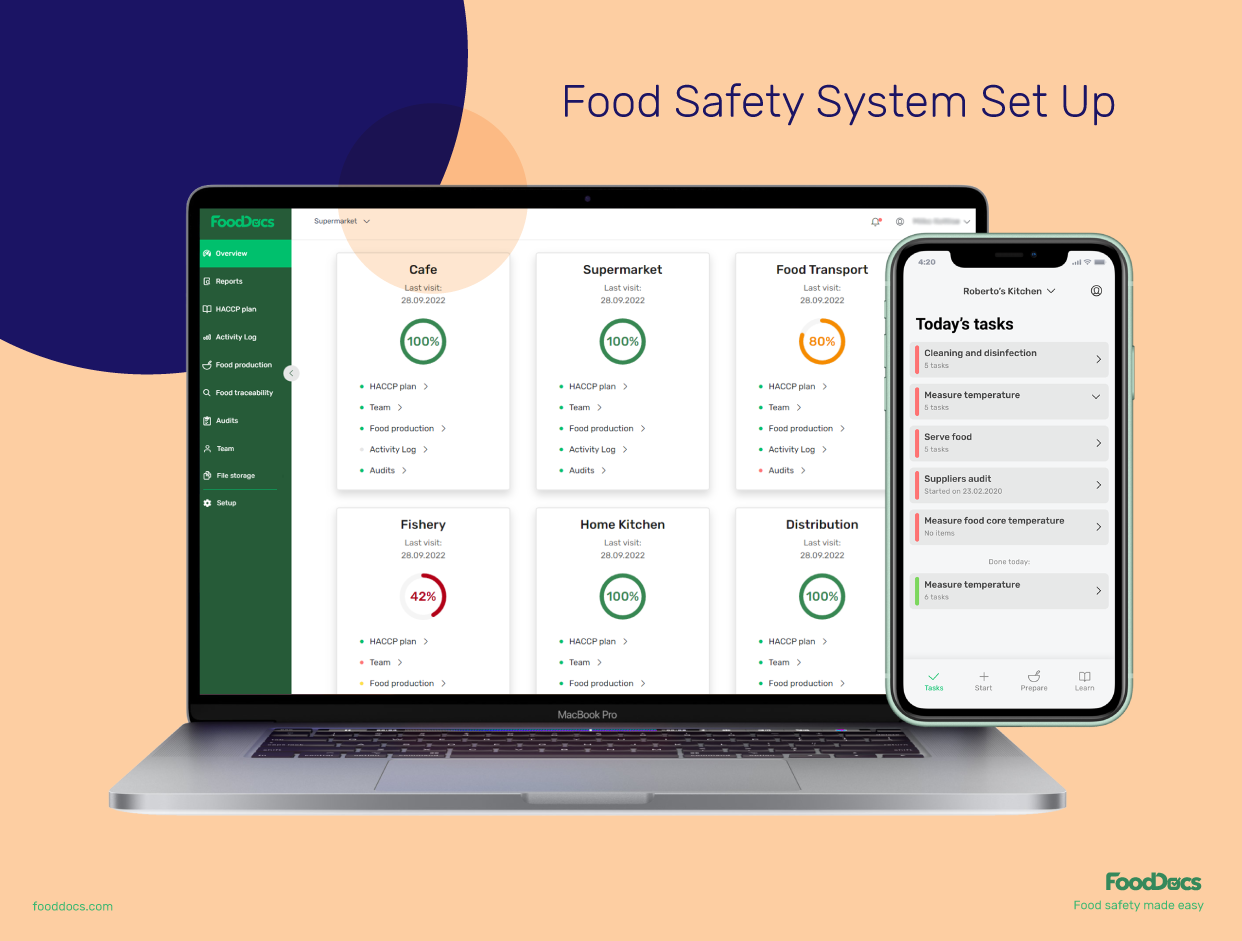
Food Safety System Set up by FoodDocs
What are food alerts?
Food alerts are formal notifications issued by official regulatory agencies informing the public and the food industry about the details of an ongoing food safety concern.
Alerts are issued when there is enough reason to believe that a food product poses a significant public health risk. It aims to inform the public of the appropriate actions to take and minimize the potential damages. These product safety alerts can be issued for a variety of reasons, including the presence of harmful bacteria, undeclared allergens, chemical contamination, or extraneous material in the food.
Food alerts can take different forms, depending on the nature of the risk and the severity of the situation. Some alerts may advise consumers to avoid or dispose of a specific consumer product. In contrast, others may recommend that certain populations, such as pregnant women or people with weak immune systems, avoid consuming a particular food altogether.
How to handle food recalls with FoodDocs?
When it comes to recalls, having the necessary information is key to a smooth recall process.
If your food business team effectively captures the essential information about every product your produce and the ingredient you use, you can easily execute a food product recall. There is a higher chance of preventing potential foodborne illnesses when you work efficiently during recalls and withdrawals.
At FoodDocs, we developed smart software that can help you prevent cases of food recalls and support you in case a food incident occurs. In a matter of minutes, our software can automatically generate all of the essential food safety documents that you need to handle food recalls.
Here are some key features that our software has to help you handle food recalls and withdrawals:
- Our system can intuitively generate a customizable digital Recall Log, which you can use to log the necessary information during a recall process. This log also features the key instructions on how to conduct a product recall process.
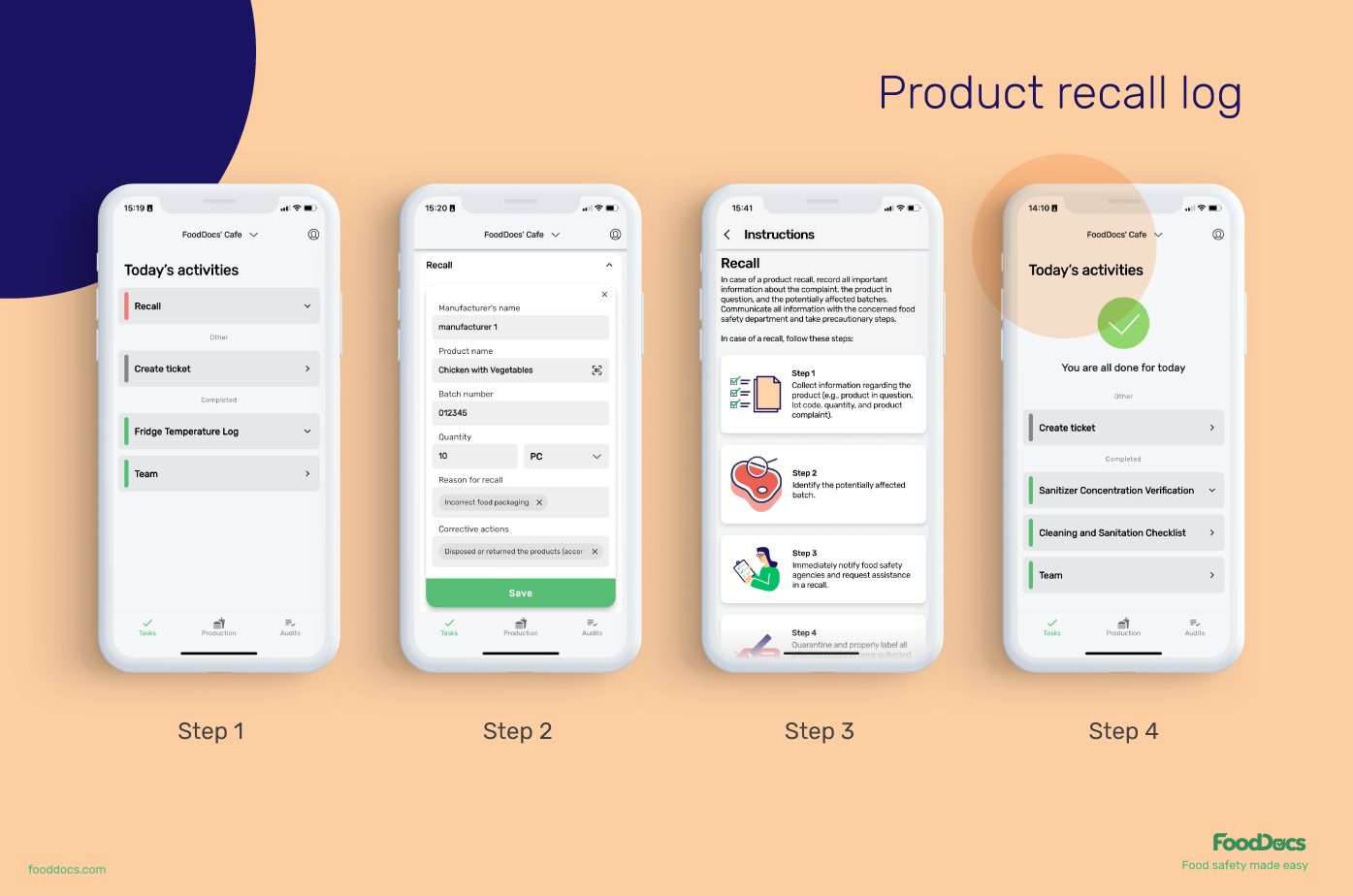
Product recall log from FoodDocs
- Prevent food recalls by ensuring that every food safety control step in your operation is followed by using automatically generated monitoring logs and checklists. These logs and checklists are equipped with corrective action solutions that are shown in case you log a non-compliant value.
Some of the logs that you can use to prevent recalls include the following:- Cooking temperature log
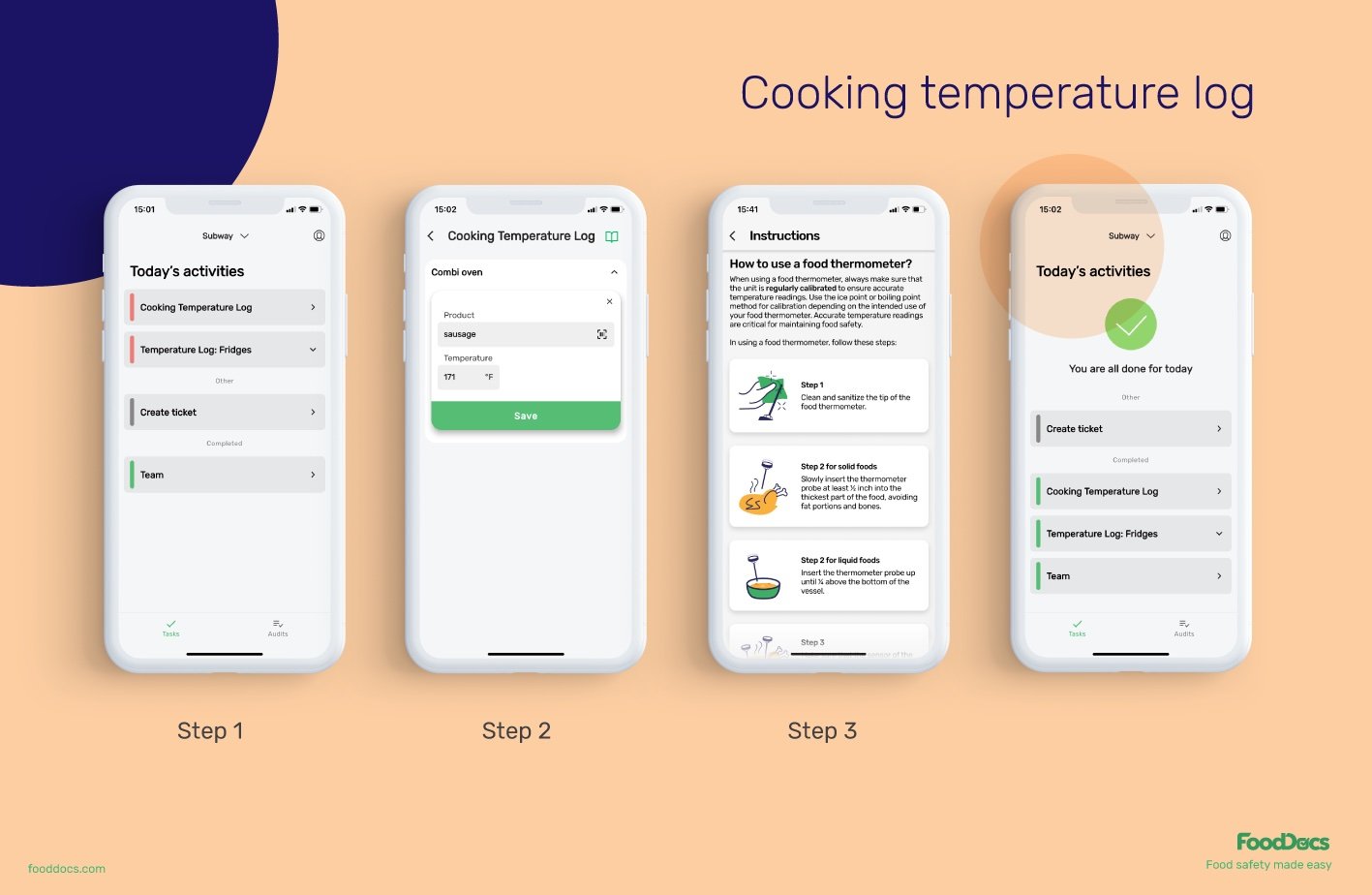
Cooking temperature log from FoodDocs
-
- Fridge temperature log
- Employee hygiene checklist
- Water testing log
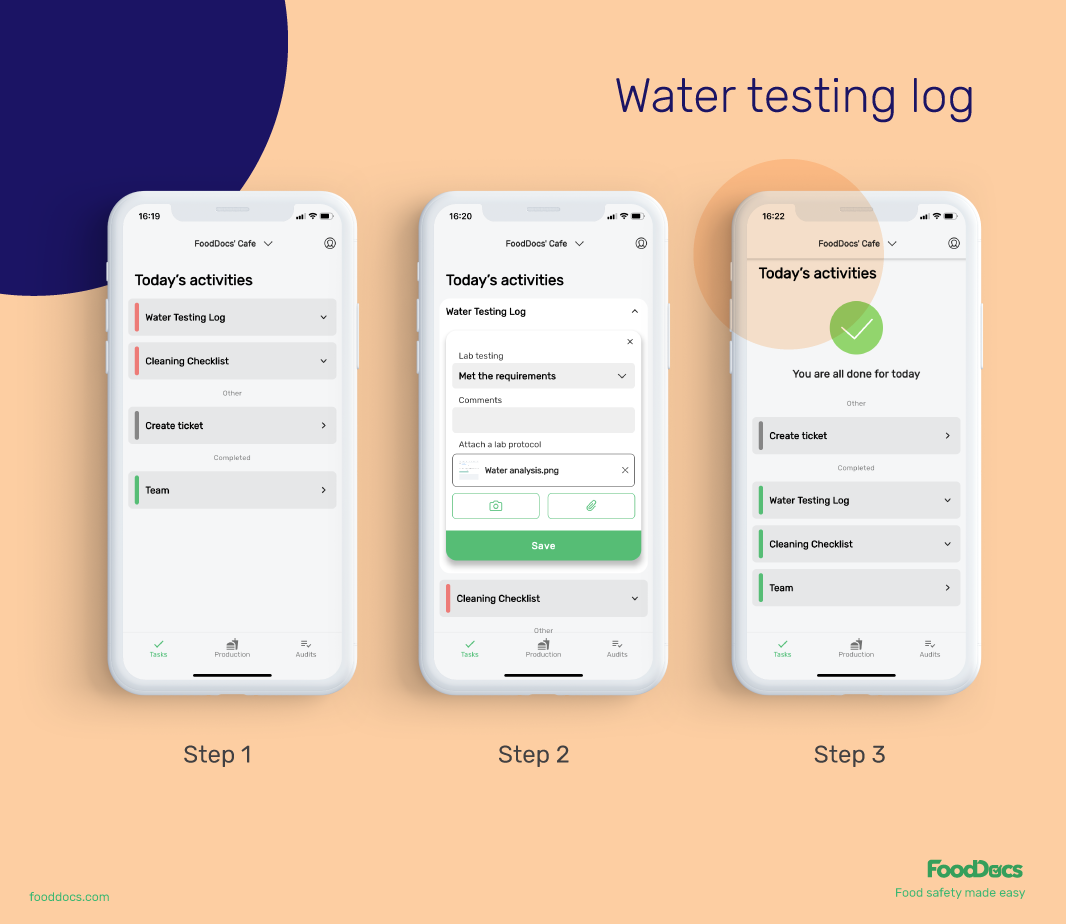
Water testing log from FoodDocs
- To help you access key information, you can use our built-in Traceability System. It can be used to log shelf-life information, product details, and allergen information. Use a Traceability System to identify affected products in a recall process quickly.
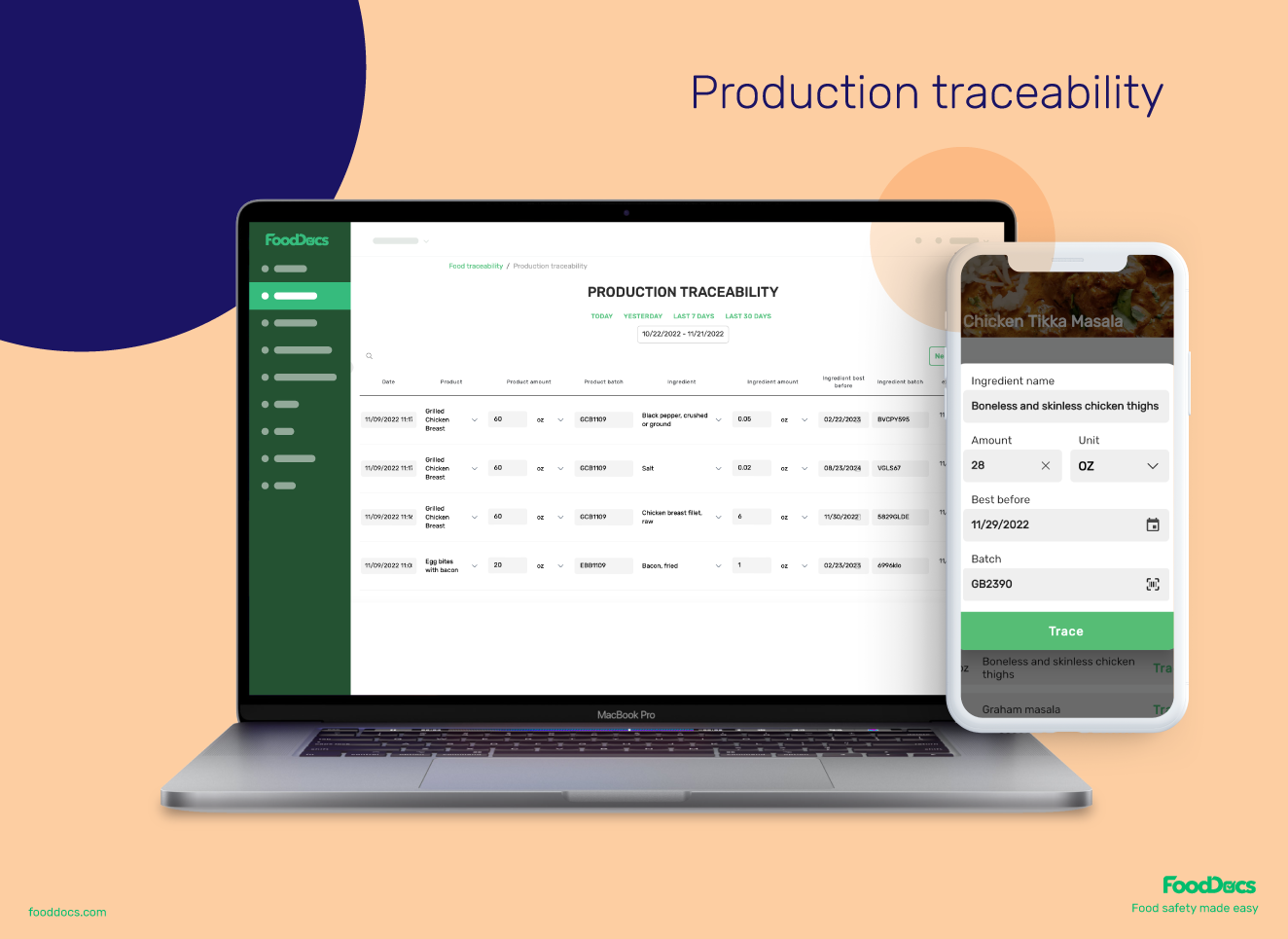
Production Traceability System from FoodDocs
- Stay on top of every recall step using our smart notification system. Our intuitive software can send alerts to employees in charge to remind them of tasks that need to be fulfilled.
In addition to key features that will help you handle or prevent food recalls, our smart software also has systems that can help you improve overall management efficiency.
- Get a real-time dashboard that gives you an overview of your entire food safety progress. Identify areas that need more attention across your different branches and save time on managing them manually.
- Store and manage all digital information in one cloud storage. You can access any information in one place at any time. Use this feature in case of a recall to provide supporting documents to food safety agencies easily.
Using our digital solutions, you can significantly minimize the chances of recalling products from the market and optimize your operations.
Improve every monitoring log and checklist that we provide by simply customizing them according to your needs. Ensure successful recall management by implementing our smart Food Safety Management System. Use our free 14-day trial to experience and explore our software features.
Frequently Asked Questions (FAQs)
Do you have more questions about food product recalls? We gathered frequently asked questions about this topic and answered them for you.
What is a food recall?
A food recall is an action taken by a food manufacturer, distributor, or retailer to remove a product from the market because it may be unsafe for consumption or does not meet regulatory standards. This can be initiated by the implicated company or by a regulatory agency, such as the FDA in the US or the FSA in the UK.
What is the difference between a food recall and food withdrawal?
A food withdrawal refers to when unsafe food is removed from the marketplace before it reaches the customers. On the other hand, a recall refers to the definitive action taken by food businesses to remove a product that is already in the market once sufficient evidence has been gathered regarding the product's safety.
Food withdrawal procedures do not need a legal sanction to be initiated. A business can issue a food withdrawal and cease distribution as a precautionary measure. Perhaps one of the most notable examples of food withdrawal is the case that led to the establishment of Natasha's Law in the UK.
In this case, the involved company voluntarily withdrew its outgoing products that caused Natasha's death from sale after the incident and subsequently made changes to its labeling policies to improve allergen information for customers.
What is food withdrawal in the US?
In the US, the term "food withdrawal" is generally used to refer to the voluntary removal of a food product from the market by a manufacturer or distributor rather than a formal regulatory action initiated by the US Food and Drug Administration (FDA). A food withdrawal is typically initiated when a food product is found to be non-compliant and before it reaches the consumers. Still, the risk is not considered to be serious enough to initiate a formal recall.
How do you know if a food is recalled?
Consumers can find out if a food has been recalled by checking the recall notices issued by regulatory agencies or by contacting the manufacturer or retailer directly. Some companies may also issue public notifications or post recall information on their websites or social media accounts. You can access recall information through the FDA, USDA, and FSA websites.
What are the benefits of food recalls?
Food recalls can help protect public health by removing potentially harmful products from the market, raising awareness about food safety issues, and encouraging companies to improve their quality control and safety procedures. They can also help restore customer confidence in the food supply by demonstrating that companies are taking proactive measures to address safety concerns. Lastly, food recalls can help prevent further financial losses by addressing food safety issues.
How can recalls be prevented?
The best way to prevent recalls is to implement a strict and comprehensive Food Safety Management System. This program includes proper food safety training, regular food and health inspections, detailed monitoring, a traceability system, and a standard assessment of the entire production chain.
Use our intuitive solutions from FoodDocs to minimize the risks of food significantly recalls in your business.