Imagine how your food business could scale if you could increase efficiency by 25x.
Ten hours on paper reduced to 50 minutes digitally… That’s how much time every week Captain Grappo’s Store Manager, Ruth Baker, has been able to save with FoodDocs. Having managed teams of up to 30 employees to smaller teams of five, Ruth suggests “that whether you’re a small establishment or a large establishment, FoodDocs makes food safety management so much easier.”
Overview of Captain Grappo's Ready-to-Eat meal production and retail food business
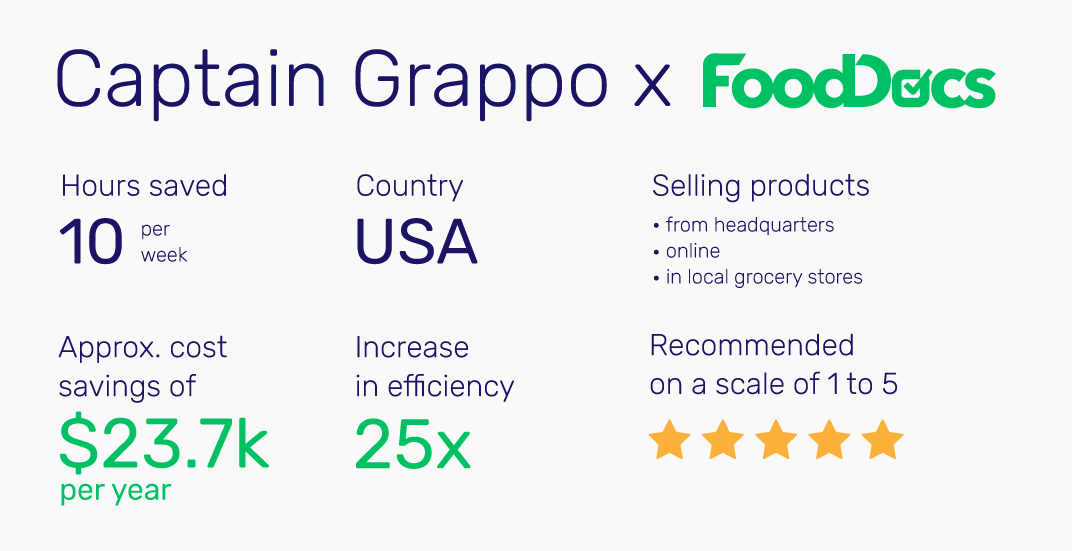
Captain Grappo is a gluten-free foods producer founded by Chad LaGrappe, who’s redefining the term “GF” to “Good Food”. It all stemmed from Captain Chad’s Celiac Disease diagnosis more than 19 years ago.
And Captain Grappo’s gluten-free food business has only kept growing!

What began as a personal journey of meticulously crafting recipes from scratch, Captain Grappo now serves some of the best fresh and frozen gluten-free cuisine. From locally sourced ingredients to beef tallow-fried food, the quality of food is matched only by the quality of Captain Grappo’s digital food safety system.
Today, they sell gluten-free foods:
- Locally out of their store in Port Arthur, Texas
- Online and delivered to homes from coast to coast
- In a grocery store chain (soon)
What did Captain Grappo’s approach to food safety look like early on?
Ruth has managed the gluten-free facility for two years. When she joined the team, Captain Grappo was a local store just breaking into eCommerce. They quickly went from handling 50 pounds of shrimp up to 700 pounds of shrimp on a regular basis. In that time, she has implemented FoodDocs and truly streamlined food safety compliance.
But it wasn’t always that way.
“Truthfully,” said Ruth, “Captain Grappo really didn't have anything in place… There wasn't a schedule of any kind, no structure in place before I got here other than all these charts that I had printed out on the computer myself.”
It’s a story many food businesses are familiar with: tiny teams, you treat your kitchen like the one at home. But as Captain Grappo began to grow, Ruth recognized the food safety risks involved with not having a proper system in place.
This was biggest food safety challenge they faced…
Ultimately, personal food safety knowledge and printed-out resources weren’t going to cut it. Small team or not, if there’s no system there’s no safety.
Daily, these questions were running through Ruth’s mind: Are we monitoring time and temperature? Are we cooling the shrimp properly? Are we frying it to the right temperature? Are we holding our hot foods at the right temp? Is everybody cleaning as they're supposed to? Washing their hands properly?
So Ruth and Chad “started to look for a system that could combine all food safety tasks into one place where [they] could monitor it. Not just for myself, but so the team could get their hands in and everybody could plug in, hey, I checked the temperatures, I logged the freezer times, whatever the task."
Why did you choose FoodDocs over other solutions?
As Ruth said, “It’s a nice, easy, simple software.”
There were a few other food safety software that Captain Grappo explored, but “they weren’t very feasible. With FoodDocs, we were able to pay and it was done… I just showed Chad and said this one does it all. I mean, it literally does it all. We can even put our recipes in here and it'll keep it stored for us and he really liked that. It was just one source, everything all in one.”
It’s not just management who like FoodDocs either. The staff do too, because it’s “accessible and simple to use.”
How was the change management from a paper-based to a digital food safety system?
There was a degree of change management involved for both management and the rest of the team.
“The transition involved mostly just getting into a routine. Because again, I think with time you get complacent and comfortable in what you're doing… [FoodDocs] has really made it a nice centralized, structured thing for us that we can actually keep up. Everybody just pitches in and now I think that they’re more hands on with that, it really helped them to get involved and see that this is something that’s important.”
FoodDocs’ onboarding and ongoing support has also helped.
“It was really nice that somebody was actually one-on-one with me and when I needed to ask questions. I still feel that one-on-one even now after using the software for so long. So it's really been nice to have somebody walk me through and get me familiar with the system, and show me a video clip on how to do that.”
The transition was fast, taking only three weeks to get everyone using FoodDocs
Ruth is a leader who, when transitioning to something new, needs it to happen quickly. She believes “the longer you stay with something that you’re familiar with, the harder it is to get away from the old ways.”
So when transitioning to a FoodDocs and making it part of the food safety culture, she ensured that onboarding her team took “three weeks for everybody to get nice and comfortable.”
Ruth shared that getting her team up to speed involved a combination of shadowing and reminding. In Captain Grappo’s current facility, Ruth and her team sit together so it’s easy to quickly, face-to-face, show them what her food safety monitoring process looks like.
Early on in the transition, being able to show her team FoodDocs’ Monitoring Log with the red and green completion graph was hugely beneficial.
“We don't want red. We want green,” said Ruth. “My team doesn’t really see what someone else may or may not have done. So it's really nice to be able to show them my screen.”
What took Ruth the longest was generally getting into a new routine. But now, she says:
“It’s nice that now I don't have to remind anybody of their food safety tasks. They even let me know, hey, it's that time to check temperatures, for example. Being able to have food safety monitoring through FoodDocs has really made it easy because the team members can just access it on their phones and do their part.”
FoodDocs’ customizable Monitoring System has set up Captain Grappo’s team for success
Team members can more accurately and quickly complete food safety tasks
FoodDocs’ Monitoring tasks are the feature that Captain Grappo uses most. It “makes it really simple for the team because it’s just a matter of opening your phone, going through your daily checklist, inputting information or just checking off what you did.”
There are times when someone is in the middle of taking an order and they have to check the temperature or the sanitizer. But now:
“They can complete those tasks without having to come back to the office, find the paperwork, grab a pen, go back out on the floor, fill it, and then bring it back to the office. It's just so accessible and a nice, simple way to get things done.”
Managers can be more efficient with their time and budget
Ruth acknowledges the harsh reality for food businesses right now.
“The cost of doing business is astronomical. Every penny matters. Paper, ink, time, and dealing with a small staff… it's all hands on deck, everybody's got to get involved. If I've got to get in there and help them with the tamales or gumbo, then I need to be able to do that. So moving to FoodDocs really helped us in the fact that I wasn’t in the back office monitoring and verifying this all manually and potentially realizing I forgot something.”
That can be a huge waste of time, money, and resources.
“It's really nice that with FoodDocs, I can plug in some things that I know I need because you input your information in the beginning setup process and then the software starts to build the system for you. Things that I didn't think of, FoodDocs was already automatically setting up for us. It really helped with time management because I had those things easily and readily accessible. So that’s definitely been something that has saved not only money but time.”
Captain Grappo gains more time and keeps more money for the business thanks to FoodDocs
When food safety was still handled on paper, Ruth typically spent a couple of hours per day getting the papers and going around checking or completing tasks.
“Now I can sit down and it's just all there in one place. It takes me 5-10 minutes. Whereas before, I had to run around with my papers and try to figure out which sheet went to what section and that kind of thing.”
10 minutes a day versus 120 minutes day? That’s a 25x increase in efficiency. On a monthly and yearly timeline, that’s respectively 60 hours and 720 hours saved in labor that would otherwise be spent on paper-based food safety management.
From a financial perspective, using a U.S. Quality Manager’s average hourly rate of $45.67, FoodDocs digital Food Safety Management System helps save the equivalent of $23,738 over a year.
FoodDocs’ Food Safety System gives Captain Grappo confidence during inspections
Captain Grappo Gluten-Free Foods is approved by the FDA. They’re also in the process of getting USDA approval.
But a HACCP Plan was always something that Ruth had inherited. She never had to create one on her own, so FoodDocs “has been a lifesaver because it took the little bit of knowledge that I had in the hands-on part of the business and plugged in all the formal stuff that I didn’t have.”
Since Ruth began managing Captain Grappo, they’ve had a couple of inspectors visit their facility and they “really liked this setup… [They] like that the HACCP system is broken down the way it is. It's really simple to read and takes you down the line in detail.”
The controlled food safety document access is also another feature that Ruth finds value in.
“I can easily share the HACCP plan with them. They're able to access it, get into it and look over it.”
What advice would you give businesses like yours that are looking for the right food safety management software?
Reflecting on a previous multinational company she managed stores for, Ruth can’t believe they still use paper-based food safety management systems.
“Using this [digital] system, I’m thinking ‘Why do you not have FoodDocs?’ This is crazy. It can all be online so that it can be shared… It’s a huge chain so I’m just like ‘Why are you back in the times of paper?’ I think it’s wild that it’s not something that more people aren’t onto because it makes life simpler.”
You can assign food safety tasks to specific people and having the employee’s name there outlines what they did (or didn’t) do.
“On the monitoring tasks for example, you can create those to cater for what your business is which is really nice because my monitoring tasks may not be the same for someone else’s because I have to make sure that what you bring in here is gluten-free… Even though [FoodDocs] is for kitchens or processing plants or whatever, in general, you can cater it to what you need to fit for your business.”
“When you’re using FoodDocs, the accountability is there. Simplification of tasks is there. Being able to verify that your employees are doing what needs to be done is there. And it's all in one place. So for somebody who's managing a business, that's a great thing. And a tool like FoodDocs that's going to help you keep everything in a schedule, keep it organized, give you some kind of a structure for your team, it’s a must.”
Curious about how you can achieve similar successes to Captain Grappo?
Start a 14-day free trial today to explore FoodDocs yourself or book a personalized demo with our team!
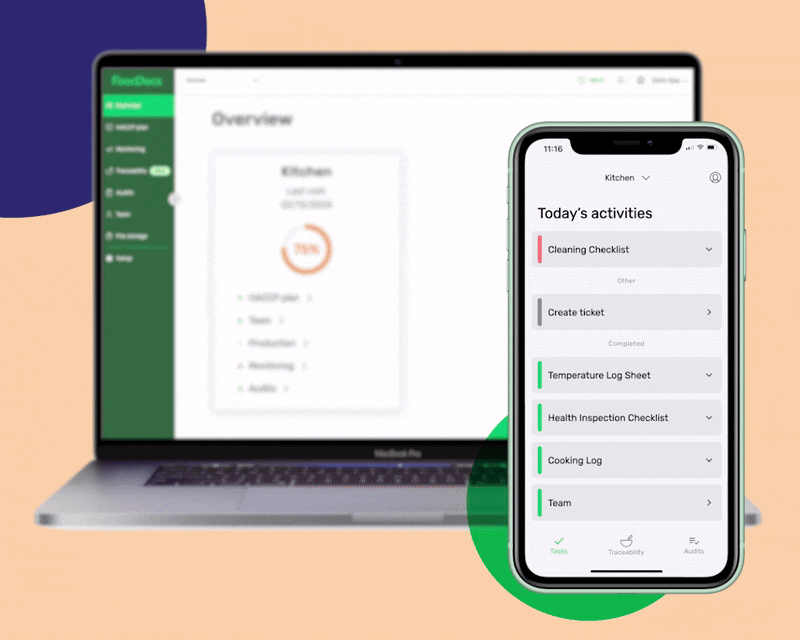
During the demo, we'll walk you through the following:
- How to switch from a pen-and-paper system to a digital solution in 15 minutes
- How to customize your daily tasks according to your company's exact needs
- How to access all monitoring and traceability data in the cloud dashboard to have an overview
- How to track deviations in your process flow
- How to maintain the same standards across all your business sites
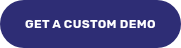